Third Party Inspection
Third Party Inspection
Third Party Inspection
Third Party Inspection
Advanced NDT Services.
We offer a range of cutting-edge Non-Destructive Testing (NDT) methods for plant inspections. Our advanced NDT services include Phased Array Ultrasonic Testing, Time of Flight Diffraction, and Eddy Current Testing.
Our highly trained and certified technicians use the latest equipment and techniques to deliver accurate and reliable inspection results. Our advanced NDT methods provide a deeper level of analysis, allowing us to detect even the smallest defects in your plant equipment.
Have a Question?
We understand that downtime can be costly, which is why we are committed to providing fast and efficient services. Our advanced NDT services help you quickly identify any issues with your plant equipment, allowing you to make informed decisions about repairs or replacements.
Our advanced NDT services are suitable for a range of industries, including aerospace, automotive, and manufacturing.
Contact us today to learn more about how our advanced NDT services can help you maintain the safety and efficiency of your plant equipment.
Phased Array Ultrasonic Testing
Ultrasonic phased array testing is a powerful NDT technology and one whose use is growing rapidly, however it can seem complex to a person who has not worked with it. This self-guided tutorial is a basic introduction to ultrasonic phased array testing, both for newcomers and for more experienced users who want a review of basic principles. It begins with what phased array testing is and how it works, then outlines some considerations for selecting probes and instruments, and ends with links to phased array application notes and a phased array glossary. In addition to text and illustrations it includes a series of interactive Flash files as learning tools.
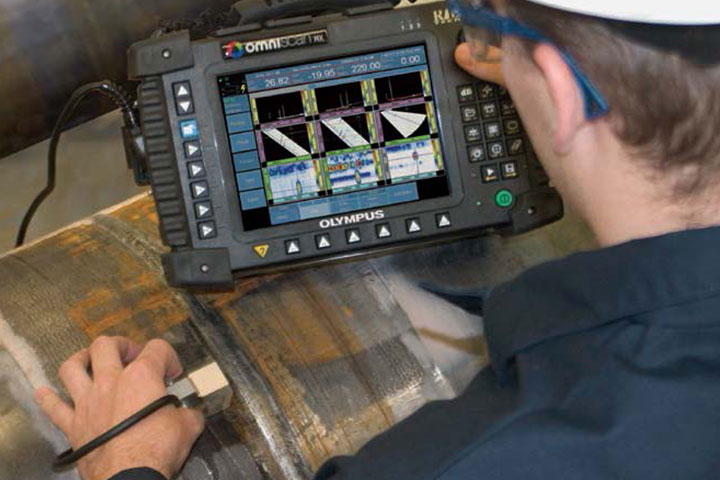
The benefits of phased array technology over conventional UT come from its ability to use multiple elements to steer, focus and scan beams with a single transducer assembly. Beam steering, commonly referred to sectorial scanning, can be used for mapping components at appropriate angles. This can greatly simplify the inspection of components with complex geometry. The small footprint of the transducer and the ability to sweep the beam without moving the probe also aids inspection of such components in situations where there is limited access for mechanical scanning. Sectorial scanning is also typically used for weld inspection. The ability to test welds with multiple angles from a single probe greatly increases the probability of detection of anomalies. Electronic focusing permits optimizing the beam shape and size at the expected defect location, as well as further optimizing probability of detection. The ability to focus at multiple depths also improves the ability for sizing critical defects for volumetric inspections. Focusing can significantly improve signal-to-noise ratio in challenging applications, and electronic scanning across many groups of elements allows for C-Scan images to be produced very rapidly.
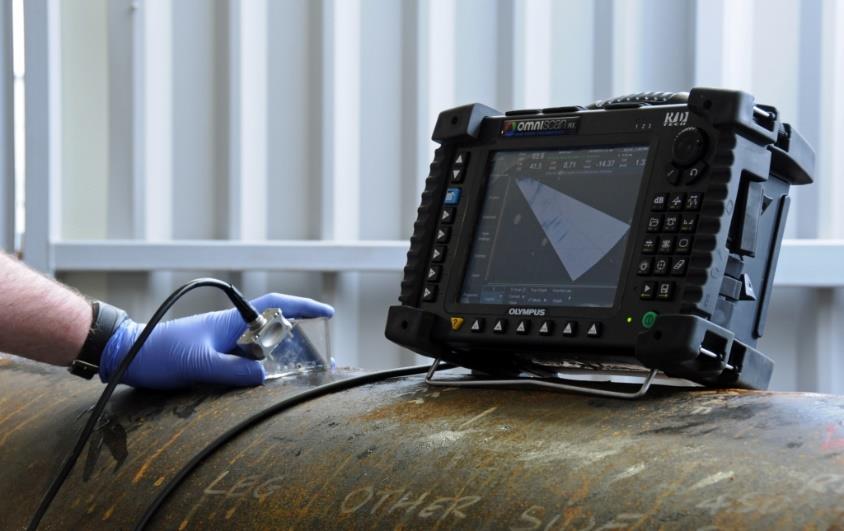
Applications
Weld inspection – Structural / Piping. Corrosion Mapping. High Temperature PAUT up to 200°C (Weld Inspection / Corrosion Mapping). PAUT in lieu of Radiography Testing (ASME Sec VIII, API 620, ASME B31.3, B31.1).
Personnel Qualification
PCN,CWSIP,ASNT Level 2/3.
Time of Flight Diffraction (TOFD)
Time of Flight Diffraction or TOFD, is one of the most promising ultrasonic techniques for the examination of welds on pressure vessels in lieu of radiography; for pipe weld quality or crack detection and also weld root erosion. TOFD is a computerised ultrasonic system able to scan, store, and evaluate indications in terms of height (through wall thickness), length and position, with a degree of accuracy and speed never achieved with other ultrasonic techniques.
TOFD consists of a separate ultrasonic transmitter & receiver. The probes are aimed at the same point in the weld volume. The entire weld is then flooded with ultrasound allowing inspection of the weld. After emission of a compressional wave from the transmitter, the first signal to arrive at the receiver is the lateral wave or OD wave which represents the outer surface or OD. In the absence of defects, the second signal to arrive at the receiver is the L-wave backwall echo which represents the inner surface or ID. When a flaw is present, a diffracted sgnal is generated at the upper tip of a defect and will arrive before the signal generated at the lower tip of a defect. With a time of flight of each flight path, ultrasonic velocity and the spatial relationship of the two probes, the location and height of the defects can be accurately calculated. Gray scale imaging techniques are applied to the RF (AC) signal phase and enables weld integrity to be observed in real time.
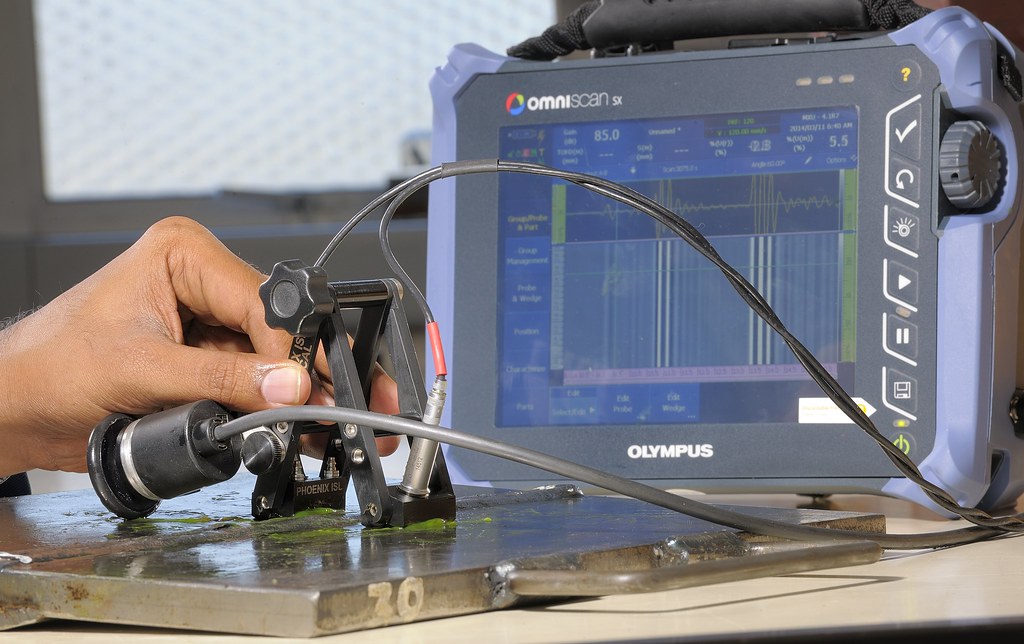
Applications
Weld inspection – Structural / Piping.
ToFD in lieu of Radiography Testing (ASME Sec VIII, API 620, ASME B31.3, B31.1).
Personnel Qualification
PCN, CSWIP, ASNT Level 2/3
Eddy Current Testing (ECT/IRIS/MFL/RFT/NFT)
Eddy Current Testing is a noncontact method used to inspect nonferromagnetic tubing. This technique is suitable for detecting and sizing metal discontinuities such as corrosion, erosion, wear, pitting, baffle cuts, wall loss, and cracks in nonferrous materials.
The Ultrasonic IRIS option is used to inspect a wide range of materials including ferrous, nonferrous, and nonmetallic tubing. This technique detects and sizes wall loss resulting from corrosion, erosion, wear, pitting, cracking, and baffle cuts.
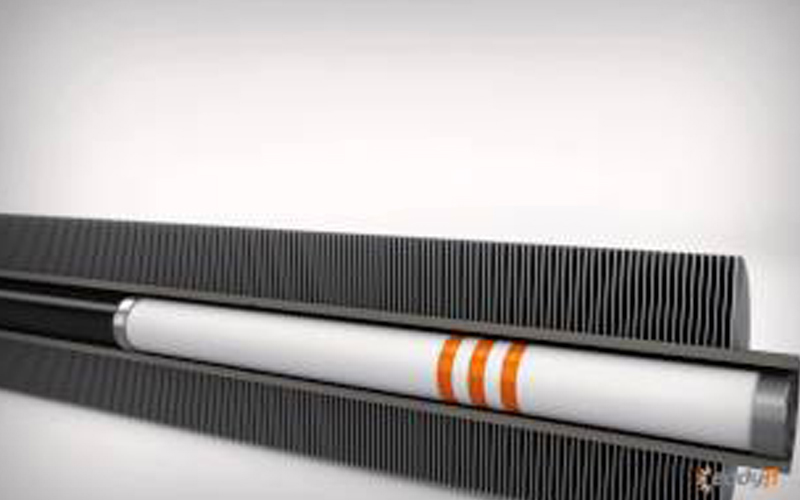
Remote Field Testing (RFT) is being used to successfully inspect ferromagnetic tubing such as carbon steel or ferritic stainless steel. This technology offers good sensitivity when detecting and measuring volumetric defects resulting from erosion, corrosion, wear, and baffle cuts. Olympus remote field probes and the MultiScan™ MS 5800 are used to successfully inspect heat exchangers, feedwater heaters, and boiler tubes, around the world.

The Near Field Testing (NFT) technology is a rapid and inexpensive solution intended specifically for fin-fan carbon steel tubing inspection.
NFT is specifically suited for the detection of internal corrosion, erosion, or pitting on the inside of carbon steel tubing. The NFT probes measure lift-off or “fill factor” and convert it to amplitude-based signals (no phase analysis).nBecause the eddy current penetration is limited to the inner surface of the tube.

Magnetic Flux Leakage (MFL) is a fast inspection technique, suitable for measuring wall loss and detecting sharp defects such as pitting, grooving, and circumferential cracks. MFL is effective for aluminium-finned carbon steel tubes because the magnetic field is almost completely unaffected by the presence of such fins.
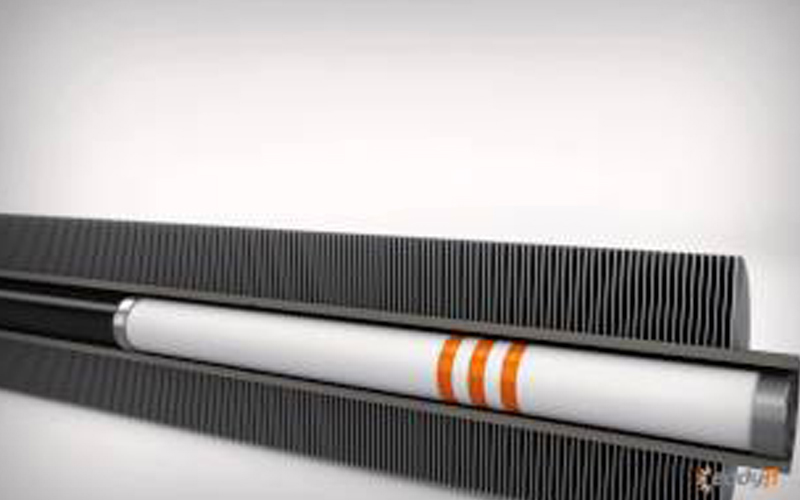
Request a Quote
Trust and Worth
Our Clients
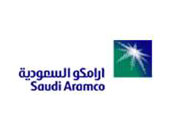
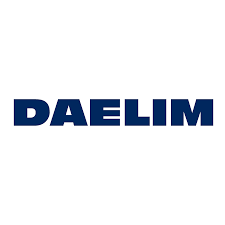
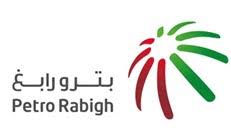
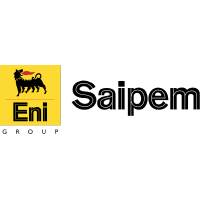
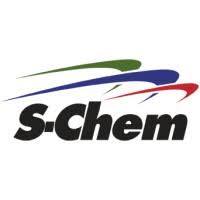
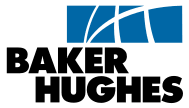
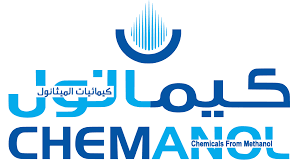
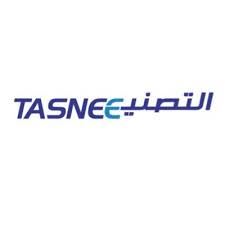

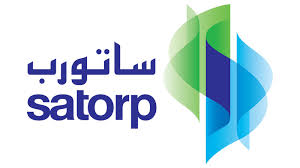
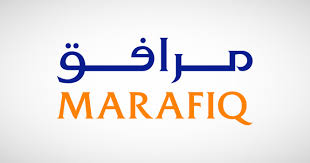
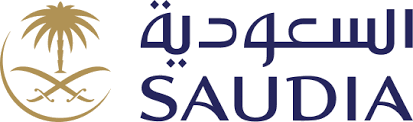